Emulsion
Note on Emulsion
Bitumen emulsion plays a pivotal role in various construction and road-building applications, offering versatility and ease of use compared to traditional hot-applied bitumen. Here’s a breakdown of key points regarding bitumen emulsion based on the provided information:
Thermoplastic Properties of Bitumen: Bitumen exhibits thermoplastic behavior, transitioning from a thin liquid at high temperatures to a solid-like consistency at ambient temperatures. This property makes it suitable for various applications, especially in the temperature range of 140 to 230°C, where it maintains a viscosity of around 200 cSt (20 Pa.$).
Modification Methods: To adapt bitumen properties for specific applications, two primary methods are commonly employed: emulsification with water and dilution with hydrocarbon solvents. These modifications enable bitumen to be applied at lower temperatures, enhancing safety and reducing environmental impact.
Bitumen Emulsion Composition: Bitumen emulsion is a heterogeneous system consisting of bitumen and water, stabilized by an emulsifier. The emulsifier prevents separation by forming electrostatic charges, holding bitumen droplets (ranging from 0.5 to 5 microns in diameter) in suspension within the continuous aqueous phase.
Classification of Bitumen Emulsions: Bitumen emulsions are categorized based on the overall particle charge imparted by the emulsifier:
-
- Cationic Emulsions: Bitumen droplets carry a positive charge and migrate towards the cathode.
- Anionic Emulsions: Bitumen droplets carry a negative charge and migrate towards the anode.
- Nonionic Emulsions: Bitumen droplets are neutral and do not migrate towards either pole. Clay emulsions are an example of nonionic emulsions.
Historical Development: The use of bitumen emulsions dates back to 1906 when S.C. Hade van Westrum patented the application of bituminous dispersions in water for road building. Initially, mechanical methods were attempted to form emulsions, but stability was achieved only with the addition of emulsifiers. Early emulsifiers were naturally occurring organic acids in bitumen, which were stabilized by adding sodium or potassium hydroxide to the aqueous phase.
Bitumen emulsion technology continues to evolve, offering enhanced performance and sustainability in various construction applications, including road paving, pavement sealing, and waterproofing.
Production Method
The production of bitumen emulsion involves several steps and requires careful control of various parameters to achieve the desired properties. Here’s an overview of the typical production process:
- Preparation of Water Phase: Water is treated with an emulsifying agent, which is a surfactant or surface-active agent, along with other chemicals as needed. These chemicals may include stabilizers or additives to enhance the emulsion’s performance or durability.
- Introduction of Bitumen: Bitumen, typically heated to a suitable temperature to ensure fluidity, is introduced into the water phase. The emulsifying agent helps disperse the bitumen into tiny droplets within the water.
- Colloid Mill Processing: The bitumen-water mixture is then passed through a colloid mill. This mill applies mechanical shear forces to break down the bitumen droplets into smaller sizes, typically in the range of microns. The emulsifying agent migrates to the interface between the bitumen and water, forming a protective layer around the bitumen droplets to prevent coalescence.
- Storage and Quality Control: The resulting bitumen emulsion is pumped to a storage tank for further processing or immediate use. Quality control measures are implemented to ensure the emulsion meets the desired specifications, including viscosity, particle size distribution, and stability.
- Variability and Chemistry: The production process involves various variables, including the type and grade of bitumen, the specific emulsifying agent used, and the emulsion formulation. Good chemistry practices are essential to optimize these variables and achieve the desired emulsion properties.
- Classification: Bitumen emulsions are classified globally into two main types: anionic and cationic. The type of emulsifying agent used determines the classification. Anionic emulsions have negatively charged droplets, while cationic emulsions have positively charged droplets. The choice between these types depends on factors such as application requirements and aggregate compatibility.
- Emulsifying Agent Chemistry: Emulsifying agents play a crucial role in stabilizing the emulsion. These agents have both hydrophilic (water-loving) and lipophilic (oil-loving) parts, allowing them to interact with both water and bitumen. This dual nature enables the emulsifying agent to form a stable interface between the two immiscible phases, preventing separation.
In summary, the production of bitumen emulsion involves combining bitumen with water and emulsifying agents, subjecting the mixture to mechanical processing, and controlling various parameters to achieve the desired properties. Good chemistry practices and quality control measures are essential to ensure the emulsion meets performance requirements for its intended application.
SLOW | MEDIUM | RAPID | Time of Setting : Charge |
CSS | CMS | CRS | Positive Charge |
ASS | AMS | ARS | Negative charge |
Characterstics of Emulsion
Bitumen emulsions play a crucial role in road construction and maintenance, offering advantages such as ease of application, workability at ambient temperatures, and controlled breaking and setting properties. Understanding the chemistry and behavior of anionic and cationic emulsions is essential for achieving the desired road surface characteristics.
In anionic emulsions, negatively charged asphalt droplets are applied to a negatively charged road surface, necessitating the breakage of the emulsion primarily through water evaporation. As water evaporates, asphalt particles come closer together until they coalesce into a continuous asphalt layer, securing the aggregate in place.
On the other hand, cationic emulsions involve positively charged bitumen droplets applied to a negatively charged surface, leading to immediate attraction and subsequent breaking of the emulsion. In addition to water evaporation, the attraction between bitumen droplets and the surface accelerates emulsion breaking, making cationic emulsions break faster than anionic ones.
Various factors influence emulsion stability and breaking, including the type and quantity of bitumen emulsifier, water evaporation rate, bitumen quantity, globule size, and mechanical forces during application. Achieving the optimal viscosity is crucial for effective application, with excessive bitumen content beyond 60% potentially leading to viscosity issues.
By understanding the chemistry and behavior of bitumen emulsions and considering factors like weather conditions, aggregate condition, and emulsion type, road construction and maintenance projects can achieve the desired outcomes of moisture sealing, skid resistance, and minimal disruption to traffic flow.
Bitumen emulsions vary in their setting time, which refers to the duration it takes for bitumen particles to separate from water after application onto aggregates. This setting time is crucial for the emulsion’s performance in road construction and maintenance. There are three main types of bitumen emulsions based on their setting time:
- Rapid Setting Emulsion (RS):
- Rapid setting emulsions have a short setting time, indicating that bitumen particles separate from water quickly after application.
- RS emulsions are suitable for situations where rapid binding and early strength development are required, allowing for faster completion of road works.
- Medium Setting Emulsion (MS):
- Medium setting emulsions have a moderate setting time, falling between rapid and slow setting types.
- MS emulsions offer a balance between rapid binding and extended workability, making them suitable for a wide range of road construction applications.
- Slow Setting Emulsion (SS):
- Slow setting emulsions have a longer setting time compared to rapid and medium setting types.
- SS emulsions provide ample time for proper spreading and penetration into aggregates before bitumen separation occurs, making them suitable for applications where prolonged workability and enhanced penetration are desired.
It’s important to note that the term “setting” in this context refers to the time taken for bitumen particles to separate from water and spread onto the aggregate surface, rather than the attainment of strength. Understanding the setting time of bitumen emulsions allows for the selection of the most appropriate type based on specific project requirements and conditions.
Emulsion grade | Cationic | Anionic | set | Minimum asphalt content | Notes |
SS-1 | * | Slow | 57 | ||
SS-1h | * | Slow | 57 | ||
QS-1h | * | Slow | 57 | Meet ASTM D3910 | |
CSS-1 | * | Slow | 57 | ||
CSS-1h | * | Slow | 57 | ||
CSS-1hP | * | Slow | 57 | Whith 3% polymer | |
CQS-1h | * | Slow | 57 | Meet ASTM D3910 | |
MS-1 | * | Medium | 55 | ||
MS-2 | * | Medium | 65 | ||
MS-2h | * | Medium | 65 | ||
CMS-2 | * | Medium | 65 | ||
CMS-2h | * | Medium | 65 | ||
HFMS-1 | * | Medium | 55 | High float | |
HFMS-2 | * | Medium | 65 | High float | |
HFMS-2s | * | Medium | 65 | Whith 1-7% solvent | |
HFMS-2h | * | Medium | 65 | High float | |
RS-1 | * | Rapid | 55 | ||
RS-2 | * | Rapid | 63 | ||
CRS-1 | * | Rapid | 60 | ||
CRS-2 | * | Rapid | 65 | ||
CRS-2P | * | Rapid | 65 | Whith 3% polymer | |
HFRS-2 | * | Rapid | 63 | High float |
NOTE
h designates a harder emulsion residue penetration between 40 and 90 DMM at 25C
s designates a requirement that the emulsion also contains solvent or distillate.
Chemicals present in the emulsion
Emulsifying Agents
In the process of producing asphalt emulsions, hot asphalt is mixed with water and emulsifier in a high-speed mixer known as a colloid mill. The colloid mill subjects the mixture to intense shear forces, which effectively breaks down the asphalt into small droplets.
As the asphalt is introduced into the mixer, it undergoes dispersion due to the high shear forces generated by the mill. At the same time, the emulsifier, typically in the form of soap molecules, is added to the mixture. The combination of shear forces and emulsifier molecules facilitates the breakup of the asphalt into tiny droplets.
The emulsifier molecules play a crucial role in stabilizing the asphalt droplets in water. They reduce the surface tension between the asphalt and water, preventing the droplets from coalescing and recombining. This results in a stable emulsion where the asphalt droplets remain dispersed throughout the water phase.
The small size of the asphalt droplets achieved through this process enhances the surface area available for interaction with aggregates during application, promoting better adhesion and coating of the aggregate surfaces. Additionally, the uniform dispersion of asphalt droplets ensures consistent performance and characteristics of the emulsion during application and curing.
How are bitumen emulsions made?
Working Procedure
History
The history of bitumen emulsion dates back to the early 1900s when it was first developed. By the 1920s, asphalt emulsions began to see widespread use in paving applications. Initially, they were primarily used for spray applications and dust control purposes.
Interest in bitumen emulsions surged in the 1950s, particularly for the construction of farm-to-market roads. However, it wasn’t until the environmental movement of the 1970s that there was a significant increase in emulsion manufacturing. This was driven by concerns about pollution from cutback asphalts, specifically volatile organic compounds (VOCs).
The advent of new formulations has led to enhanced performance across various applications. These formulations have addressed specific challenges and requirements, further expanding the versatility and effectiveness of bitumen emulsions in construction and maintenance projects.
What is Bitumen Emulsion?
How Emulsifiers Work
Anionic Emulsifier Structure
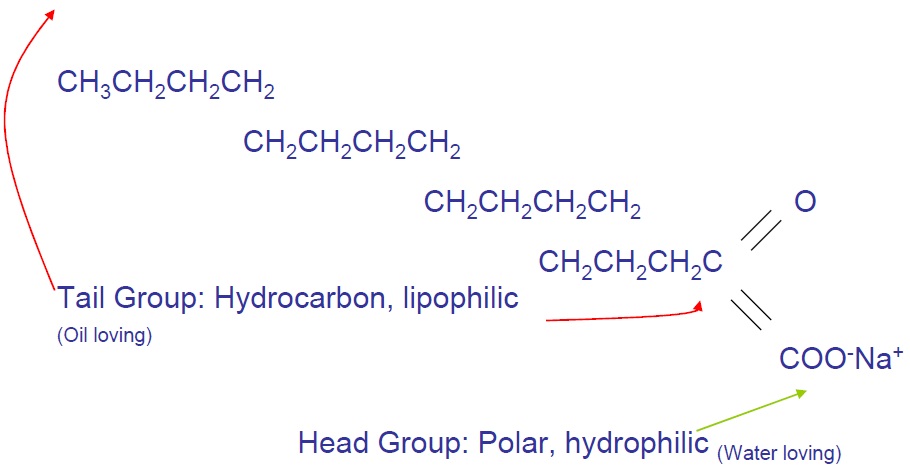
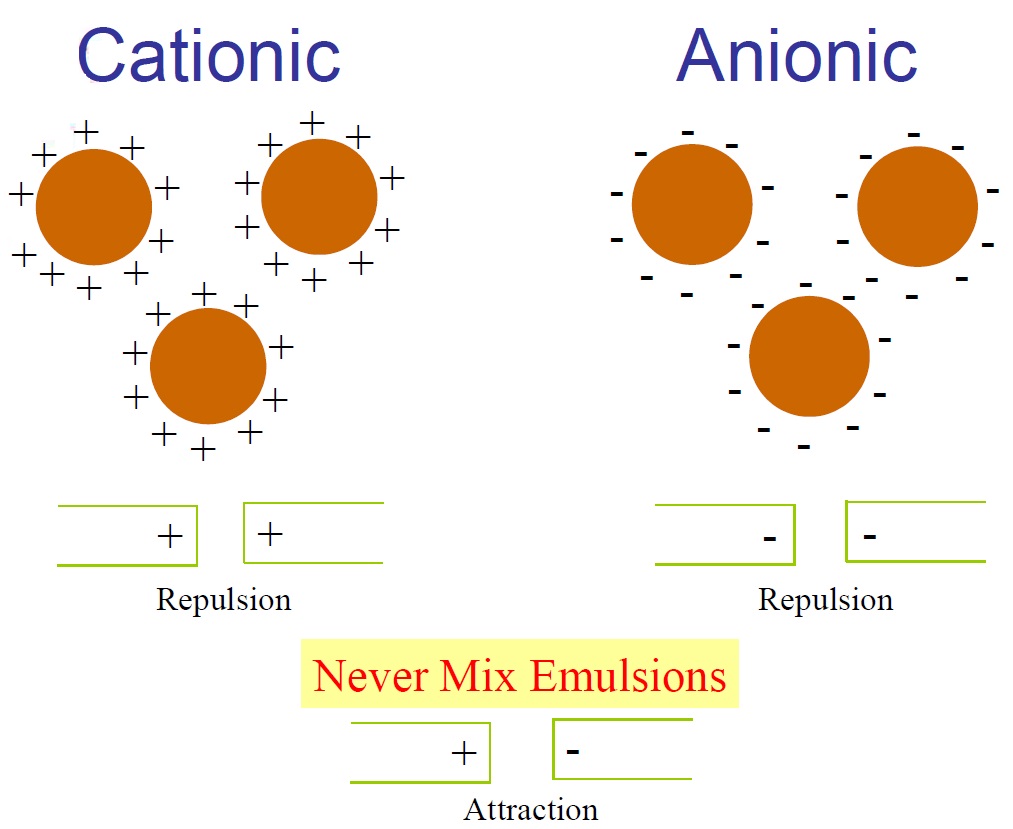
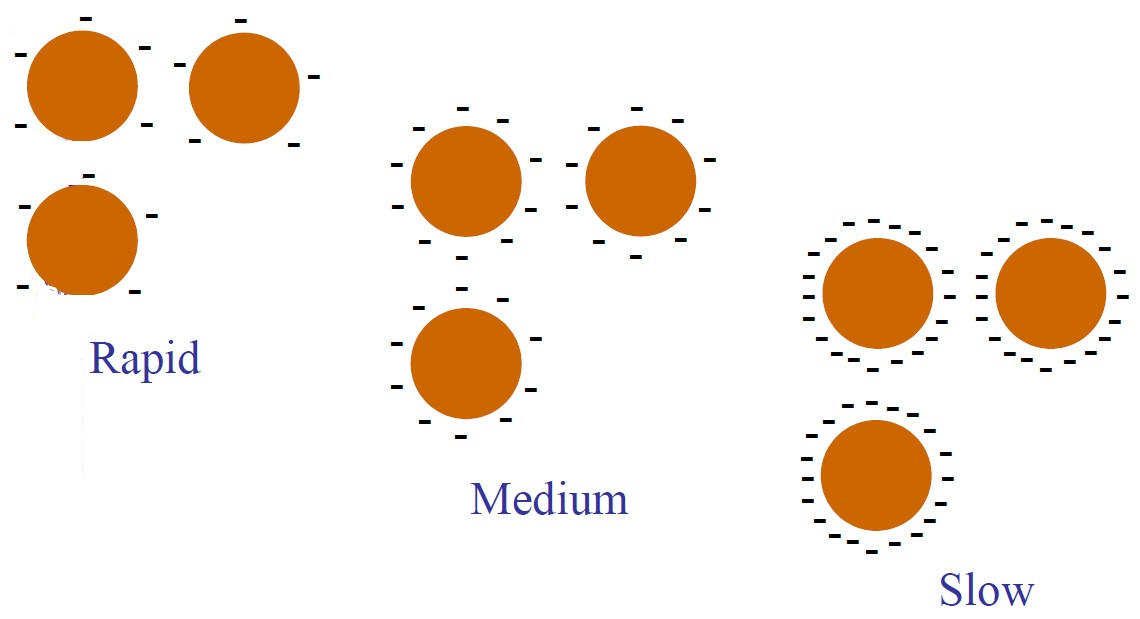
Naming the Emulsion
Here’s how the naming convention for bitumen emulsions typically works:
Prefix:
- RS = Rapid Set
- SS = Slow Set
- QS = Quick Set
- MS = Medium Set
- HFRS = High Float Rapid Set
- C = Cationic
- AE = Anionic Emulsion
Suffix:
- 90, 150, or 300 = Penetration Ranges
- h = Hard Penetration
- P, M, or L = Modified with Polymer or Latex
- 1 = Low Viscosity, Stored at Cooler Temperatures
- 2 = High Viscosity, Stored at Higher Temperatures
Putting it all together, an example name might look like “RSSS-150M”, which would indicate a cationic emulsion with a slow set, designed for a penetration range of 150, modified with polymer or latex, and having medium viscosity, suitable for storage at higher temperatures.
For Example
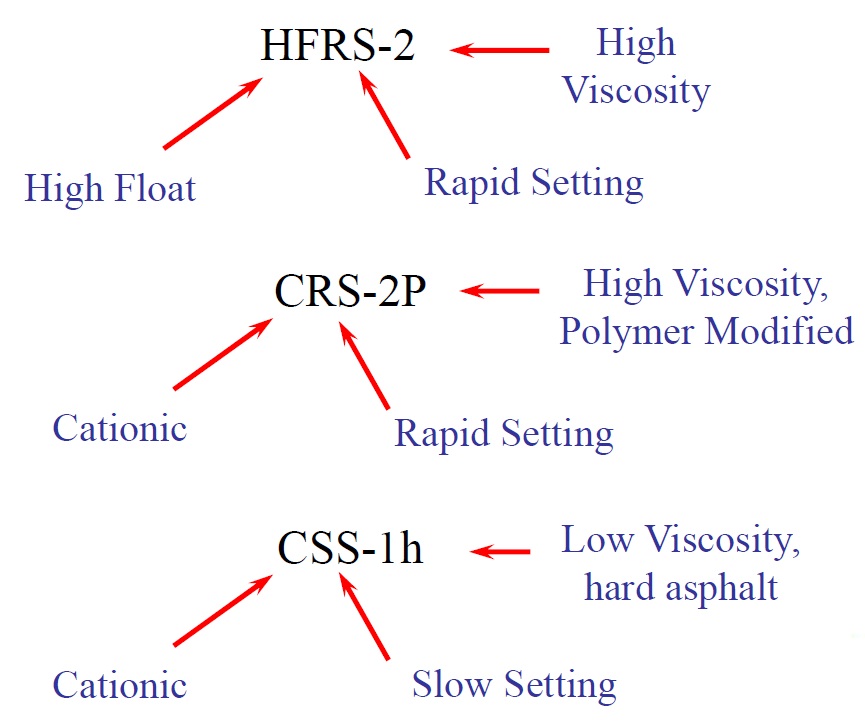
Modifications
Certainly, polymers like SBS (Styrene-Butadiene-Styrene) and SBR (Styrene-Butadiene Rubber) are commonly used to modify bitumen emulsions for road construction. Here’s how these modifications enhance the properties of the emulsion:
-
Increased Service Life: The addition of polymers, such as SBS and SBR, introduces large molecules into the bitumen, enhancing its durability and resistance to aging and weathering. This modification extends the service life of the asphalt pavement, reducing maintenance needs and lifecycle costs.
-
Early Chip Retention: Modified bitumen emulsions exhibit improved adhesion to aggregate surfaces. This early chip retention capability ensures that the aggregates remain securely embedded within the asphalt layer during construction, reducing the risk of aggregate loss and enhancing the overall pavement performance.
-
Flexibility: Polymers impart greater flexibility to the asphalt mixture, enabling it to withstand temperature fluctuations and traffic loads without cracking or rutting. This flexibility is particularly important in regions with extreme weather conditions, where asphalt pavements are subjected to thermal cycling and heavy traffic loads.
-
Elasticity: The presence of polymers enhances the elasticity of the bitumen emulsion, allowing it to deform and recover under stress. This property helps prevent the development of cracks and fatigue in the pavement, ensuring long-term structural integrity and ride quality.
In summary, polymer modifications in bitumen emulsions significantly improve the overall performance of asphalt pavements, enhancing their durability, adhesion, flexibility, and resistance to distress mechanisms.
General Classification
Certainly, here’s a general classification of bitumen emulsions based on their setting characteristics and common applications:
-
Rapid-Setting (RS): These emulsions have a fast setting time and are designed to react quickly with aggregates, reverting from the emulsion to asphalt rapidly. They are typically used for applications where quick curing and traffic reopening are essential. Examples include patching, surface treatments, and certain types of pavement repairs.
- Examples: RS-2, HFRS-2
-
Medium-Setting (MS): Medium-setting emulsions have a moderate setting time, offering a balance between rapid curing and extended workability. They find use in various construction and maintenance applications, such as tack coats, chip seals, and slurry seals.
- Example: MWS-90
-
Slow-Setting (SS): Slow-setting emulsions have a longer setting time, providing extended workability and allowing for precise application. They are commonly employed in surface treatments and seal coats where a slower curing process is desirable to achieve optimal adhesion and durability.
-
Quick-Setting and Micro-Surfacing (QS): Quick-setting emulsions are formulated for rapid curing, making them suitable for applications like micro-surfacing, where quick traffic reopening is critical. They are also used in cold mix applications and certain types of surface treatments.
- Example: CRS-2
Medium Setting Emulsion
Bitumen emulsions designed for mixing with graded aggregate. Here’s an explanation of their characteristics and common applications:
- Designed for Mixing with Graded Aggregate: These emulsions are specifically formulated to be mixed with graded aggregate to produce asphalt mixtures for various construction applications.
- Extended Workability: Unlike rapid-setting emulsions, these emulsions are formulated not to break immediately upon contact with the aggregate. Instead, they remain workable for a period ranging from a few minutes to several months, depending on the specific formulation and project requirements.
- Primary Use in Pugmills: Pugmills are commonly used to mix bitumen emulsions with aggregates. These emulsions are well-suited for use in pugmills, where the mixture can be thoroughly blended to achieve the desired consistency and workability.
Examples of such bitumen emulsions include:
- MS-2 (Medium-Setting)
- CMS-2 (Cold Mix)
- HFMS-2 (High Float Medium-Setting)
- MWS-150 & MWS-300 (Medium-Setting with specific penetration ranges)
These emulsions find applications in various projects requiring asphalt mixtures, such as road construction, pavement maintenance, and patching, offering extended workability and versatility in mixing with different types of aggregates.
Slow-Setting Emulsion
Bitumen emulsions specifically formulated for mixing stability and used primarily with high fine content aggregates, tack coats, fog seals, and dust palliatives. Here’s a breakdown of their characteristics and applications:
- Mixing Stability: These emulsions are engineered to provide excellent mixing stability when combined with aggregates, ensuring uniform distribution and adhesion of the bitumen throughout the mixture.
- Primary Use with High Fine Content Aggregates: They are ideally suited for use with aggregates containing a high proportion of fine particles. This makes them suitable for applications where such aggregates are common, such as tack coats, fog seals, and dust palliatives.
- Applications:
- Tack Coats: Used to bond pavement layers together, improving adhesion between existing and newly laid asphalt layers.
- Fog Seals: Applied to the surface of existing asphalt pavements to rejuvenate and seal the surface, reducing oxidation and water infiltration.
- Dust Palliatives: Applied to unpaved surfaces to suppress dust and stabilize the surface, enhancing safety and reducing environmental impact.
Examples of such bitumen emulsions include:
- SS-1h (Slow-Setting with hard penetration)
- Dusty (specifically designed for dust control)
These emulsions offer superior performance in applications where mixing stability, adhesion, and compatibility with fine content aggregates are crucial for achieving desired results in road construction and maintenance projects.
Quick-Setting & Micro Surfacing
Bitumen emulsions tailored specifically for slurry and micro-surfacing applications, with features geared towards quicker opening to traffic times and enhanced performance in these surface treatment methods. Here’s a closer look:
- Designed for Slurry and Micro-Surfacing: These emulsions are formulated to meet the specific requirements of slurry seals and micro-surfacing, which are thin surface treatments applied to existing pavements to rejuvenate, seal, and protect them from further deterioration.
- Quicker Opening to Traffic: The emulsions are engineered to allow for faster curing times, facilitating quicker reopening of the treated road to traffic. This attribute is particularly important for minimizing disruption and maintaining traffic flow during construction and maintenance activities.
- Polymer Modification: Micro-surfacing emulsions are often polymer-modified, enhancing their performance and allowing for the placement of thicker layers compared to conventional slurry seals. Polymer modification improves durability, abrasion resistance, and overall longevity of the treated surface.
Examples of such bitumen emulsions include:
- CSS-1h (Cationic Slow-Setting with hard penetration)
- CQS-1h (Cationic Quick-Setting with hard penetration)
- CQS-1hM (Cationic Quick-Setting with hard penetration, modified with polymer)
These emulsions are specifically tailored to meet the stringent requirements of slurry and micro-surfacing applications, offering enhanced performance, durability, and efficiency in pavement preservation and rehabilitation projects.
Advantages of using Bitumen Emulsion
Using bitumen emulsion offers a plethora of advantages over traditional methods like hot mix asphalt and cutback bitumen. Here’s a summary of these advantages:
- Elimination of Heating Process: Bitumen emulsions can be used at ambient temperatures, eliminating the need for energy-intensive heating processes, which reduces energy consumption and associated costs.
- No Chemical Solvents: Unlike cutback bitumen, bitumen emulsions do not require chemical solvents like kerosene. This eliminates the risk of environmental contamination and reduces health and safety hazards associated with solvent use.
- Fire Safety: Bitumen emulsions pose no risk of fire during storage, transportation, or implementation, enhancing safety in handling and application.
- Low Emissions: Bitumen emulsion applications produce minimal hydrocarbon emissions and fumes, making them environmentally friendly and suitable for use in non-attainment areas with strict emission regulations.
- Applicability in Various Climates: Bitumen emulsions can be applied in humid climates and at lower temperatures, offering versatility in different environmental conditions.
- Extensive Application: Bitumen emulsions find extensive application in road construction and maintenance, including surface treatments, patching, chip seals, slurry seals, and micro-surfacing.
- Versatility in Other Applications: Bitumen emulsions can be used for stabilizing shifting sands, mulching, and dust control, particularly in desert and western areas where dust exposure is a concern.
- Coating Damp Aggregate Surfaces: Bitumen emulsions readily coat damp aggregate surfaces, reducing the need for aggregate drying and minimizing fuel consumption during production.
- Pavement Preservation: Bitumen emulsion applications in pavement preservation help reduce the need for raw materials and energy for corrective maintenance and reconstruction. Additionally, smoother pavements lead to lower vehicle repair and fuel needs.
- Quality Assurance: Bitumen emulsion manufacturing and processing are overseen by skilled professionals dedicated to producing high-quality products, ensuring consistency and reliability in performance.
In summary, the use of bitumen emulsion offers numerous benefits, ranging from environmental sustainability and safety to cost-effectiveness and versatility in various construction applications.